Carbide rods are solid cylindrical pieces made from a combination of tungsten carbide and a metallic binder, typically cobalt. They are used for a variety of applications, including cutting tools for metal and wood, wear parts for machinery, and drill bits for oil and gas drilling.
The hardness and high melting point of tungsten carbide make it an ideal material for cutting and drilling applications, while the metallic binder provides the necessary toughness and durability. The combination of these properties allows carbide rods to perform well in high-stress environments and maintain their cutting edge even after prolonged use.
The manufacturing process for carbide rods involves mixing tungsten carbide powder with the metallic binder and shaping the mixture into the desired form. The resulting rods are then sintered, or heated under pressure, to fuse the material and improve its density. The final product is a tough and durable rod that can withstand high temperatures and heavy loads.
In conclusion, carbide rods are an important component in a variety of industrial applications due to their hardness, melting point, and toughness, making them ideal for cutting, drilling, and wear-resistant applications.
Grade Performances of Tungten Carbide Rod
Type | Grade | ISO | Grain Size of Wc | Content of Co | Density | Typical Hardness | TRS(/MPa) |
For Cutting | CF10 | K20/K30 | 0.8μm | 10% | 14.4g/cm³ | HRA91.8 | 3600 |
CF12 | K20-K40 | 0.6μm | 12% | 14.1g/cm³ | HRA92.3 | 3800 | |
CF25 | K05/K10 | 0.4μm | 12% | 14.85g/cm³ | HRA92.8 | 3800 | |
For Stamping | CFK3 | / | 0.8-1.0μm | 13% | 14.06g/cm³ | HRA90.8-91 | 3600 |
F7 | / | 1.0μm | 15% | 13.85g/cm³ | HRA89.3 | 3800 |
Grade | Recommend Application | ||||||
CF10 | Stable performance fine grain size material, general purpose for steel, cast iron, aluminum, copper, heat-resistant alloy etc. Suitbale for making end mills, drills, reamers etc. | ||||||
CF12 | Having high wear-resistance and excellent shock-resistance, suitbale for milling and drilling stainless steel, hardened steel, aluminum alloy, nickel base alloy etc. | ||||||
CF25 | Super-fine grain size material, It’s suitable for rough and finishing machining of die steel, stainless steel, superhard aluminum alloys, heat resistant alloy and other general materials below 60HRC. | ||||||
CFK3 & F7 | Good toughness, it’s used for stamping die, wear resistant part. |
How does Tungsten Carbide Rods Manufacture
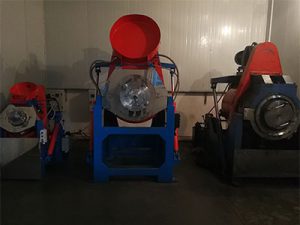
Wet Milling
We use Fine and Ultra Fine grain size of tungsten carbide powder. To control uniform grain size, wet milling is the first step.
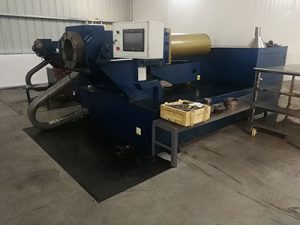
Extrusion
Before extrusion, it shoud be dried and granulated. Extrusion is the main way to press long carbide rods like 300, 310,330mm. We manage diffrent diameter carbide rods with different extrusion machine to improve production efficiency. We can manage diameter from 2-30mm.
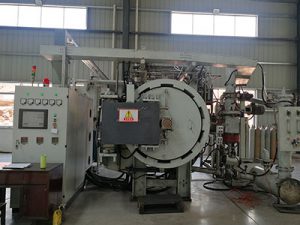
HIP Sintering
Sintered under 6Mpa pressuer and 1400℃+ .
Every batch after sintered, we will analysis firstly. Coercive force, Hardness, TRS, Density, Metallographic. To ensure the carbide rods we send to customer is qualified.
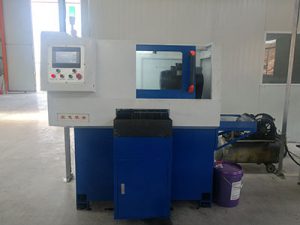
Cutting to short
The sintered tungsten carbide rods is 300-330mm standard length, The auto cutting machine was needed to cut it to standard or nonstandard short carbide rods as required like 45mm, 50mm, 150mm long etc.
The next step is Precision Grinding, we plan to add grind machine to service customer.